Atomic layer deposition for high aspect ratio (HAR) structures
It’s a small world, and it’s rapidly getting smaller, especially in emerging technologies. The tiny parts of today’s nanotechnology solutions may be just barely visible, but they have mountainous differences in surface structures, with sharp edges, steep slopes, deep trenches and gate oxides concentrated in a single area. These types of complex surfaces with high aspect ratio (HAR) features require incredibly precise processing; you want those steep slopes and deep trenches conformally protected, too.
HAR and nanotubes
Surfaces with HAR features are found for example in nanotubes. Nanotubes made from TiO2 are widely used, especially on photocatalytic applications and water purification systems. The geometry of these types of nanotubes approach very high aspect ratios, and their widely varying surface structures need conformal coating to increase lifetime and efficiency.
Reliable coating is not only crucial, it’s also demanding, and the best results are achieved with ALD coating.
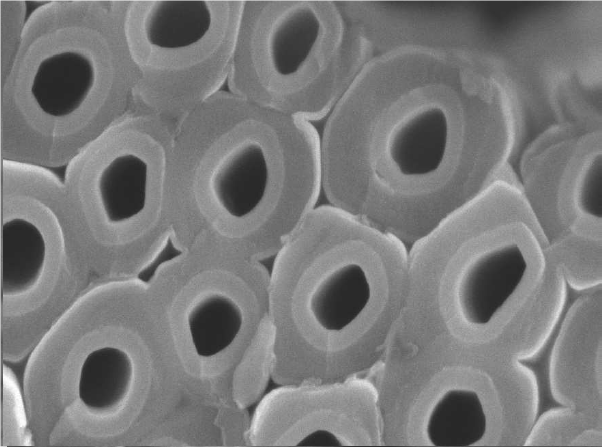

In figures 1 and 2 above are example results of Al2O3 deposition on TiO2nanotubes with an aspect ratio of 1:1088 using the Beneq HAR module. The thickness of the ALD layer is 38.8 +/- 4 nm at the middle of the nanotube and 39.8 +/- 5.7 nm at the bottom of the nanotubes. Figure 3 below shows the height of the coated nanotubes. Images courtesy of J. Prikryl et al. AVS-ALD 2016, 19.7.2016, Ireland.
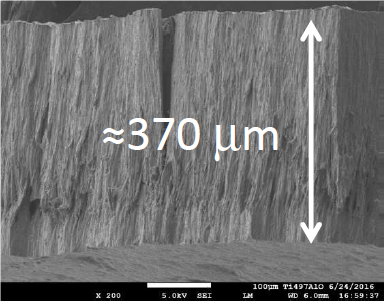
Why choose ALD for High Aspect Ratio structures?
The answer is simple, only ALD can ensure a conformal coating on HAR structures.
You could choose, let’s say, CVD coating, but you’ll only get the flatter surfaces coated, not the trenches, tunnels, steep slopes, or sharp edges. In a CVD coating process, all the chemicals are sent at once. This means that not only will you have a totally non-conformal end result, but you’ll also have gas phase reactions and uncontrolled growth.
With ALD coating processes, a gas at a time is sent in pulses. This means that everything, even the deepest tunnels, are saturated and conformally coated. Conformal ALD coating is brilliantly suited for HAR structures due to its self-limiting characteristic. This characteristic restricts the reaction at the surface to no more than one monolayer of precursor. By increasing the precursor pulse time, the precursor can disperse into those steep slopes and deep trenches, allowing for complete reaction with the entire surface.
Uniquely Beneq
At Beneq, we provide four unique qualities with our Beneq TFS 200 and HAR module combination for the best ALD coating results:
1. No cross-contamination
Our inert gas valve (IGV) system keeps even the most minor traces of precursor flow out of the reaction chamber. You don’t have to worry about contamination.
2. Wide process temperature range
Chemicals are different, and so are the processing temperatures. We deliver processing ranges from 0°C to 500°C.
3. Different gas flow configuration options
Surfaces vary; you may need cross flows, or shower head flows, or both. You have the option to choose.
4. Easy maintenance of reaction chambers
The reaction chamber is held together by pressure differentials and seals, it’s not bolted down. You can easily remove it, clean it, and put it back.
We’ll be looking more closely at the actual technology behind Beneq HAR modules in our future blog posts.
If you would like to hear more now, you are more than welcome to talk to Beneq specialists, they will happily answer your questions and queries!
If you’re not familiar with our Beneq TFS 200 systems, check out the Beneq TFS 200 product options, or contact us for more details.