- Who: Laser Zentrum Hannover
- Tool: Beneq C2R
- Market: Optical Coatings
- Use Case: Single- and multi-material antireflective (AR) coatings; AR coatings on nanostructured components
Why ALD?: ALD has advantages, including precise thickness control and high conformality, that none of the directed PVD processes can cover. This allows ALD to be used to coat complex structured, freeform and 3D optics. LZH was surprised how simple it was to adapt ALD to optical coatings and cite a small, highly curved lens as a case study. With classical PVD processes, it’s nearly impossible to achieve a conformal coating on the curved surface and the same reflection or transmission values over the whole area. With ALD, they found it so simple and easy to achieve.
Why C2R?: The C2R’s rotating mechanism allowed LZH to coat at deposition rates up to 1 µm/hour, comparable to current ion beam sputtering (IBS) processes. Speed is paramount for economic manufacturing. Furthermore, the Beneq C2R gave LZH the possibility of plasma enhancement, which offers low-temperature processing on sensitive substrates, like polymer lenses in mobile phone cameras, and can help to increase the adhesion of the coating to the surface.
Result: The inclusion of ALD into LZH’s manufacturing tool park strongly extended their coating possibilities and furthers the applications that are possible in-house. Encouraged by the potential of the tool, LZH continues to develop the C2R with Beneq and has recently implemented their own broadband monitoring system into the tool for high-resolution process control. They hope to help bring spatial ALD to the forefront of industrial optics manufacturing.
”Light for innovation”
Founded in 1986, LZH is an independent, non-profit research institute dedicated to promoting applied research in the field of photonics and laser technology. With nearly 200 employees, LZH offers solutions to current and future challenges with its smart photonics from component development for specific laser systems or quantum technologies to process developments for a wide variety of laser applications.
A few years ago, their Optical Components Department noticed a trend of new substrates, including structured and freeform optics as well as miniaturized optics for higher integration level. These emerging optics limited the usefulness of the current physical vapor deposition (PVD) processes, so they decided to seek a new solution.
“As a research institute working in the thin film technology area, we are always on the search to establish new technologies for optical applications,” says LZH’s Head of Optical Components, Dr. Andreas Wienke.
“With regard to a rising trend of structured, freeform or even 3D-printed optics, uniform PVD coatings come to the limits of their manufacturing possibilities and require rethinking of coating technologies. ALD is mainly known from the semiconductor industry sector, which has quite comparable requirements for their thin film coatings specification.”
“ALD has huge advantages in terms of thin film uniformity and extreme thickness control to basically an atomistic layer, which has made [the technology] highly interesting for us for a few years now,” Dr Wienke asserts.
ALD easily transfers to optical coatings
Each [ALD] cycle produces approximately 1 Angstrom of material, giving immense control over film thickness and the ability to deposit highly conformal films on complex 3D objects and nanostructures, like waveguides, lenses and domes. Traditional PVD processes struggle to provide antireflective (AR) and other coatings with the necessary conformality desired by optics manufacturers. These factors initially attracted the LZH team to ALD.
We were surprised by ALD’s simple adaptation to optical coatings
Dr. Andreas Wienke, LZH
LZH was soon happy to confirm that optical coatings grown with ALD performed as well as IBS according to their benchmarks. They were also taken by the ease with which ALD could be implemented.
“We were surprised by its simple adaptation to optical coatings,” says Dr. Wienke. “Think of a strongly curved, small aspheric lens. With classical PVD processes, it’s nearly impossible to achieve a conformal coating on the curved surface and the same reflection or transmission values over the whole area. With ALD, it seems so simple and easy to achieve.”
However, ALD has been historically pegged as a slow process, and without high deposition speeds, the technology would not be viable for the industry.
“High deposition rates are the key to fulfill the main drivers in the optical industry: low-cost production and high throughput,” Wienke states. The team began searching for ALD tools that might meet the challenge, and in 2018, LZH purchased a Beneq C2R.
C2R: Designed for ultrafast depositions and low-temperature processing
The Beneq C2R is a rotary spatial ALD system designed specifically for ultrafast depositions, crucial for optics manufacturers looking to use ALD in volume production, such as for mobile phone lenses, AR/VR goggles, or LiDAR devices. As a spatial tool, the C2R has a turntable which rotates samples through zones of gaseous precursor, rather than individually dosing the reactants.
With rotation speeds up to 200 rpm, films can be grown as quickly as 1 µm/hour, about 100 times faster than typical ALD processes. Dr. Wienke explained that the high deposition rate that can be achieved with the new tool is of great importance for customers as it makes manufacturing much cheaper.
“The C2R, with its rotating principle, allowed us to coat at rates already comparable to IBS processes. Hence, an economic production is possible. Together with the self-limiting effect of ALD, this promises high quality coatings,” he says.
In addition to its high deposition speed, LZH cited the significance of the Beneq C2R plasma capability that allows for the use of plasma-enhanced ALD for low temperature processing and increased film adhesion. This affords even more possibilities for its use, with the ability to coat temperature-sensitive substrates, like polymer lenses in mobile phone cameras.
LZH initially began using the C2R for single and multi-material antireflective (AR) coatings, mainly depositing tantalum oxide and silicon oxide. Now they are exploring ALD for AR coatings on nanostructured components where classical PVD processes cannot be used and expect ALD to demonstrate its advantages.
Enabling emerging optical applications
Why then is ALD little known, and even less utilized, in the optics industry? ALD appears to be tailor-made for future optical coatings. In part, it comes down to history.
PVD processes, IBS in particular, have a rich history in the optics community and have served the sector extremely well. Even LZH has been working with the technique for over 30 years and notes it as their “workhorse” for developing and manufacturing optical coatings.
“In the optical coatings community, ALD was seen more as a tool for very specific purposes that tried to compete with the established PVD processes,” explains Dr Wienke. “For a range of challenges PVD is the state of the art.”
This coupled with an initial notion that ALD is slow represented a tough barrier to overcome. But Wienke and LZH endeavor to show the opportunities ALD can offer to the optics community, seeing it not as a replacement for IBS, but as an enabling technology for emerging fields. “We see ALD technology not as a replacement of existing technologies, like IBS or e-beam evaporation. We are still conducting a lot of research on these and have many industrial customers,” Dr Wienke offers.
“ALD has advantages that none of the directed PVD processes can cover and is useful for a variety of applications. Including it in our manufacturing tool park strongly extends our coating possibilities and the further applications that are possible with it.”
In another vein, it comes down to exposure. Beneq and LZH believe the ability of the rapid spatial ALD approach to deposit conformal films is not well-known in the industry, so widespread integration has yet to be realized. Since adopting ALD, LZH has been busy on the road promoting the technology and the Beneq C2R, frequenting shows like Photonics West, Optatec and Optica OIC. So far, reception has been stellar.
“The fact that rotary ALD is really fast and still provides highly conformal layer thicknesses has generated a lot of interest. We received quite a lot of questions, inquiries and feedback from the optics community on ALD coatings after we had some presentations at international conferences and trade shows with the first results,” Wienke tells.
Working with the best and deepening relationships
Encouraged by the system’s potential, LZH continues to work closely with Beneq to develop the C2R into a premium tool for use in the optical coating industry. Recently, they implemented their own Broadband Monitoring (BBM) system into the tool for high resolution online process control, a feature commonplace on all their current coating plants, and one that will now be standard on the C2R.
With the BBM, users can keep track of their film properties in real-time and automatically adjust their deposition process on the fly. Optical coatings demand tight specifications and BBM allows for significantly better control and reproducibility over the resulting film quality. In total, the machine with all its features and the implemented BBM system promises strong benefits for future applications in the optics industry.
Dr. Wienke expressed enthusiasm for the joint industry-institute partnership between LZH and Beneq saying, “We strive for excellence and innovative solutions for our scientific and industrial partners. We are glad to be able to work with the best and be part of the development of this innovative ALD system in close collaboration with Beneq. An industry-institute relationship combines the best of two worlds, the expertise and cutting-edge knowledge of a research institute with the practical needs and want for innovation of the industry.”
The addition of ALD and the Beneq C2R makes LZH proud to offer the most diverse and powerful manufacturing capabilities to the optical coating industry. They hope the expanding interest can help them to apply for more scientific projects and continue deepening industry cooperation.
There appears to be excitement growing in the community and ALD is ripe for adoption in high volume manufacturing applications. Together with Beneq, Dr. Wienke and the LZH team strive to bring ALD to the forefront of optics manufacturing.
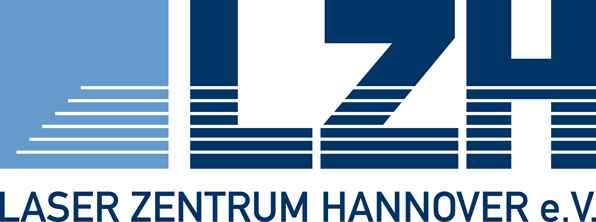