Display manufacturers are laying down the foundations for volume production of MicroLEDs, the next-generation of technology for high-resolution displays. Compared to miniLEDs, MicroLEDs are much smaller and do not use a backlight. Instead, each pixel is controlled individually, resulting in higher brightness and lower energy consumption. Since MicroLEDs are only a few microns in size, they can no longer be produced in high yields with traditional manufacturing processes. Rather, nanometer control of fabrication techniques is necessary to uniformly manufacture the millions of LEDs needed for a single display.
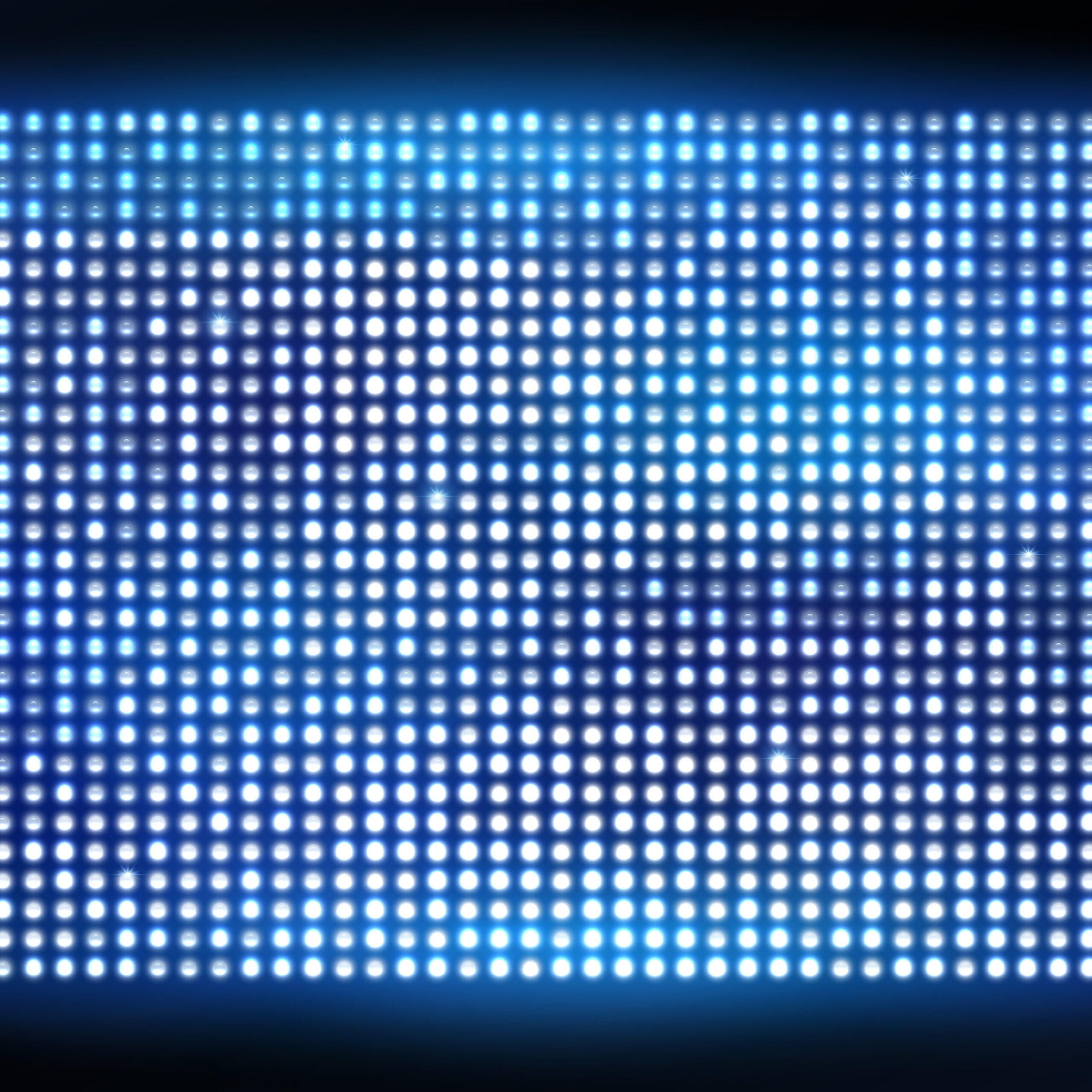
miniLED
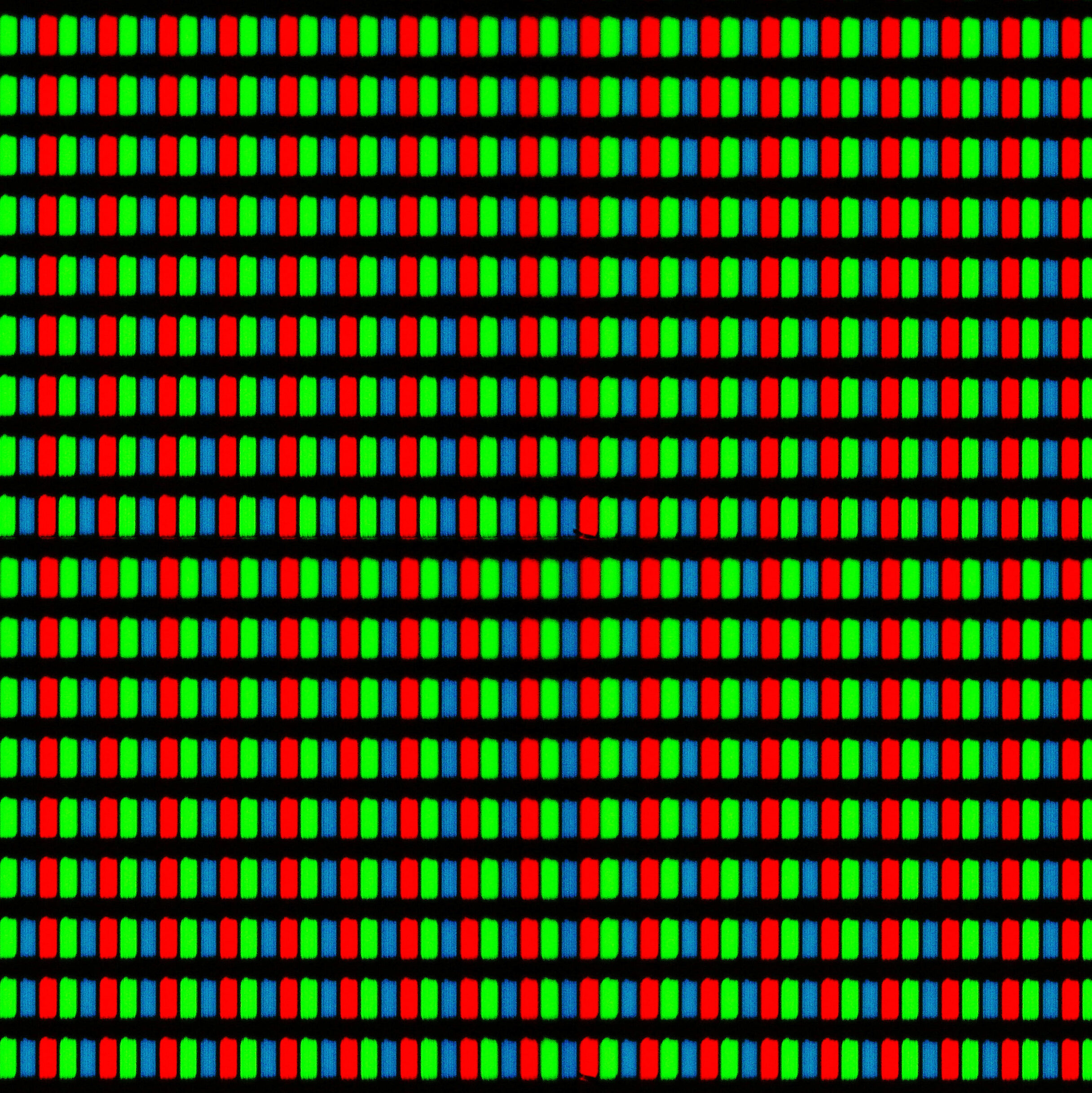
MicroLED
Size: 100-200 micrometers
Display: Backlit
Contrast: Medium
Efficiency: Medium
Response time: Low (ms)
Maturity: High
Size: < 10 micrometers
Display: Self-emissive
Contrast: High
Efficiency: High
Response time: High (ns)
Maturity: Low
Conformal surface passivation of MicroLEDs
Atomic layer deposition was an enabling technology for the miniaturization of the transistor and has the ability to enable mass production of MicroLEDs. The highly conformal films produced by ALD, for example, make it an excellent candidate for passivation of all MicroLED surfaces. Compared to established PECVD processes, using ALD gives the necessary surface coverage on high-aspect ratio structures for effective passivation, resulting in lower leakage current, higher luminous intensity, and longer lifetimes.
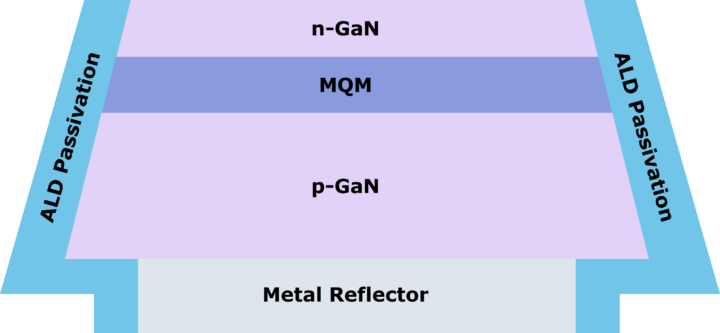
With Beneq’s cutting-edge integrated plasma and thermal ALD capability, we can optimize the passivation stack to the specific MicroLED surface e.g. for InGaN or InGaAlP surfaces.
Other ALD uses in the MicroLED manufacturing process include:
- Transparent conductive oxide (TCO) deposition
- Distributed Bragg Reflector (DBR) fabrication
- Heat dissipation layers
- Final passivation (moisture barrier)
Explore our other applications of ALD for LED & Photonics!